In the fast-paced world of modern warehousing and distribution, the efficiency of material handling processes is crucial for businesses aiming to stay competitive. One of the key elements in this realm is the utilization of advanced Conveyor and Sortation Systems. At Greenspace Industrial, we understand the significance of these systems in revolutionizing the warehousing industry, and we take pride in offering cutting-edge technologies that optimize efficiency, streamline operations, and boost productivity for businesses across North America.
Common Sorters: Sortation Systems and Conveyor Systems
Sortation Systems
Sortation systems are a vital component in the modern warehouse, providing the means to automate and optimize the sorting process. Various types of sortation systems cater to different sorting needs, each offering unique advantages in terms of speed, accuracy, and adaptability. Here are some notable types of sortation systems:
Sweeper Sorters:
- Sweeper sorters utilize a sweeping motion to divert items into their designated chutes or lanes, ensuring efficient and rapid sorting.
Cross-Belt Sorters:
- Featuring cross belts that move perpendicular to the main conveyor, cross-belt sorters are effective in handling a wide range of products and achieving high sorting accuracy.
Sliding Shoe Sorters:
- Sliding shoe sorters use sliding shoes to push items off the conveyor onto the divert lanes, providing a gentle and precise sorting method.
Tilt-Tray Sorters:
- Tilt-tray sorters involve trays that tilt to deposit items into designated chutes, creating a looping sorting process that enhances speed and efficiency.
Push Tray Sorters:
- Employing mechanical arms or push trays, this type of sortation system directs items to their designated destinations with accuracy and reliability.
Strip-Belt Sorters:
- Narrow belt or strip-belt sorters use narrow belts to carry and divert products based on predefined criteria, making them versatile and adaptable to various sorting needs.
Popup Wheel Sorters:
- Popup wheel sorters use wheels that pop up to transport and sort products to their respective destinations, providing a reliable and efficient sorting solution.
Bomb Bay Sorters:
- Bomb bay sorters operate by dropping items into designated chutes from above, ensuring a swift and controlled sorting process.
Vertical Sortation Systems:
- Vertical sortation systems involve the vertical movement of items to achieve sorting, offering a compact and space-efficient solution for warehouses with limited floor space.
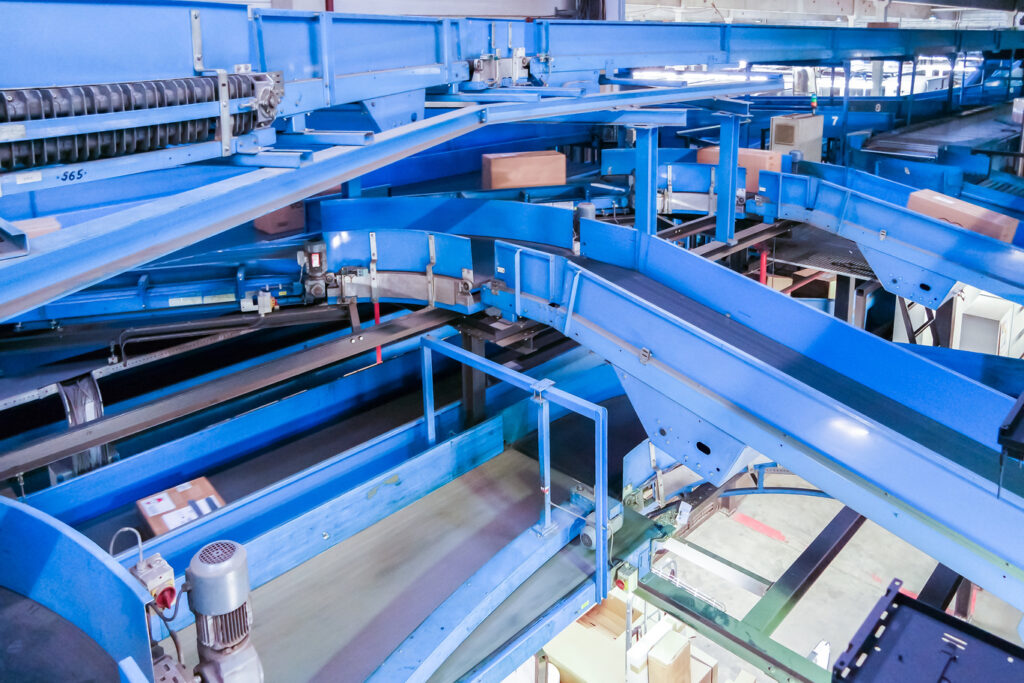
Conveyor Systems
Conveyor systems form the backbone of material handling in warehouses and distribution centers, facilitating the seamless movement of goods from one point to another. These systems come in various types, each designed to address specific needs within the supply chain. At Greenspace Industrial, we offer a comprehensive range of conveyor systems, tailored to meet the diverse requirements of modern logistics operations.
Diverse Range of Conveyor Systems
Greenspace Industrial’s repertoire of conveyor systems encompasses various types, each designed to cater to distinct operational needs:
Gravity Conveyors: Designed for efficient handling of lightweight materials, these systems leverage gravity to move items along inclined or declining paths. They offer cost-effectiveness and minimal maintenance, ideal for various industries.
Powered Conveyors: Utilizing motor-driven mechanisms, powered conveyors such as belt conveyors, chain conveyors, and roller conveyors provide enhanced control and flexibility in material handling. These systems accommodate diverse load capacities and operational demands.
Spiral Conveyors: Ideal for vertical movement of materials between different levels within a facility, spiral conveyors offer a space-saving design and efficient transport capabilities, optimizing space utilization in congested production areas.
Telescopic Conveyors: Tailored for rapid and efficient loading and unloading of goods, telescopic conveyors can extend or retract, adapting to varying truck or container lengths. They streamline material handling processes and optimize space within warehouses or distribution centers.
Vertical Conveyors: These systems facilitate the seamless vertical movement of materials between different levels, eliminating the need for inclines or declines. They are indispensable in scenarios where space optimization is critical.
Conveyor Chutes: Greenspace Industrial’s conveyor chutes ensure smooth and controlled material transfer between conveyors or into bins and containers, minimizing spillage and optimizing the flow of goods within the industrial process.
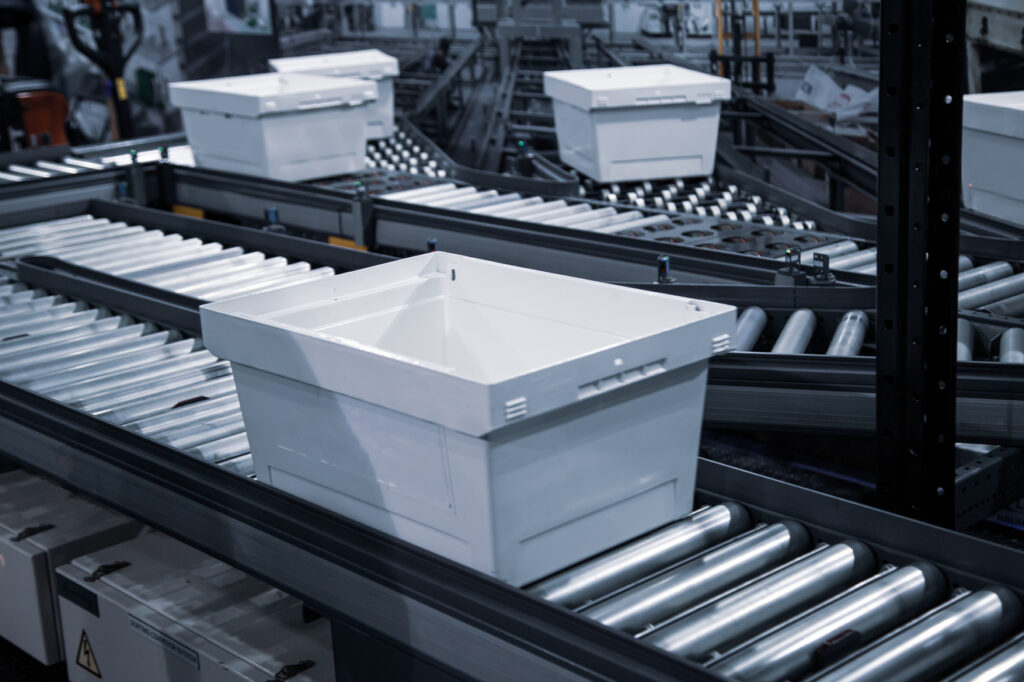
How a Sortation Conveyor Works?
A Sortation Conveyor is a specialized conveyor system equipped with mechanisms to divert or channel products to different destinations based on predefined criteria. It operates based on automated sorting algorithms, identifying products and directing them to their designated bins, chutes, or lanes. This process ensures that each product is efficiently routed to its intended location.
Advantages of a Sortation Conveyor
The implementation of a Sortation Conveyor system offers several advantages to warehouse and distribution center operations:
- Improved Efficiency: Sortation systems significantly enhance the speed and accuracy of order fulfillment, reducing processing times and increasing overall efficiency.
- Enhanced Order Accuracy: Automation in sorting minimizes the risk of human errors, leading to higher order accuracy and customer satisfaction.
- Streamlined Operations: By automating the sorting process, businesses can streamline their overall operations, resulting in increased throughput and reduced labor costs.
- Adaptability: Sortation systems are highly adaptable and can handle a diverse range of products, making them suitable for warehouses with varying inventory characteristics.
Types of Sortation Conveyor Systems
Shoe Sorter:
- Utilizes shoes or slats to divert products to designated chutes.
Narrow Belt (Strip Belt Sorters):
- Uses narrow belts to carry and divert products based on sorting criteria.
Pop-Up Wheel Sorters:
- Employs pop-up wheels to transport and sort products to their respective destinations.
Cross-Belt Sorters:
- Features cross belts that move perpendicular to the main conveyor to achieve sorting.
Arm or Pusher Style Sorters:
- Utilizes mechanical arms or pushers to direct products to sorting destinations.
Tilt Tray Sorters (Loop Sorters):
- Involves trays that tilt to deposit items into designated chutes, creating a looping sorting process.
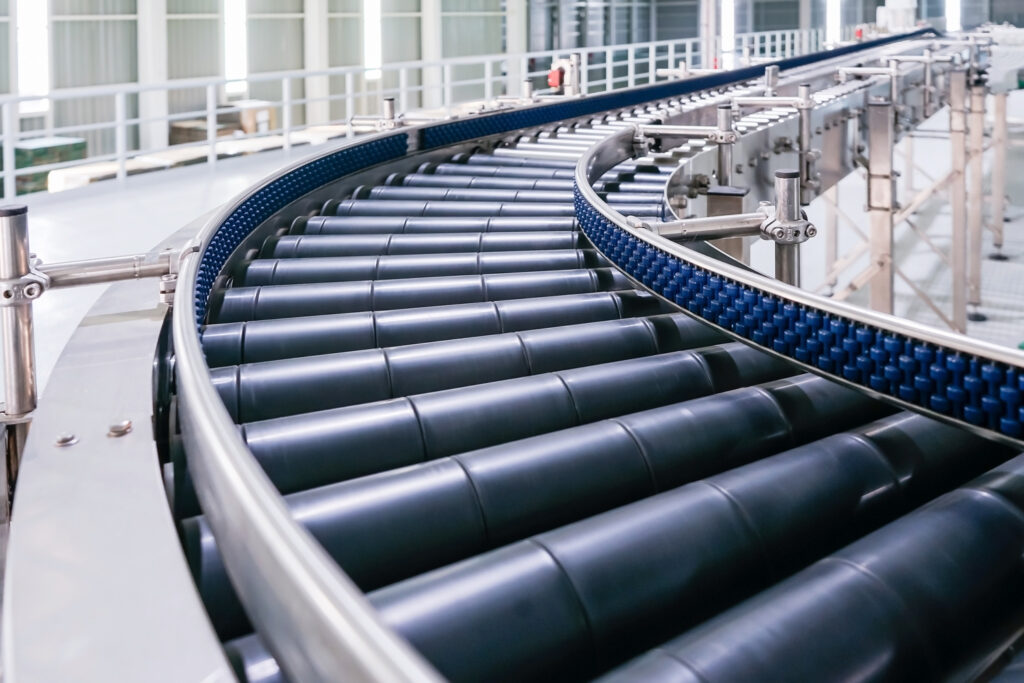
Your Next Steps for a Sortation Conveyor System
Implementing a Sortation Conveyor system involves careful consideration and planning. Here are the key steps to guide you:
Assess Your Needs:
- Identify the specific requirements of your warehouse or distribution center, considering factors such as product variety, sorting speed, and space constraints.
Choose the Right Type:
- Select the type of Sortation Conveyor system that aligns with your sorting requirements. Each type has its unique features and advantages.
Consider Integration:
- Ensure seamless integration with existing material handling systems and technologies for a cohesive and efficient operation.
Evaluate Space and Layout:
- Assess the available space and layout of your facility to optimize the installation of the Sortation Conveyor system.
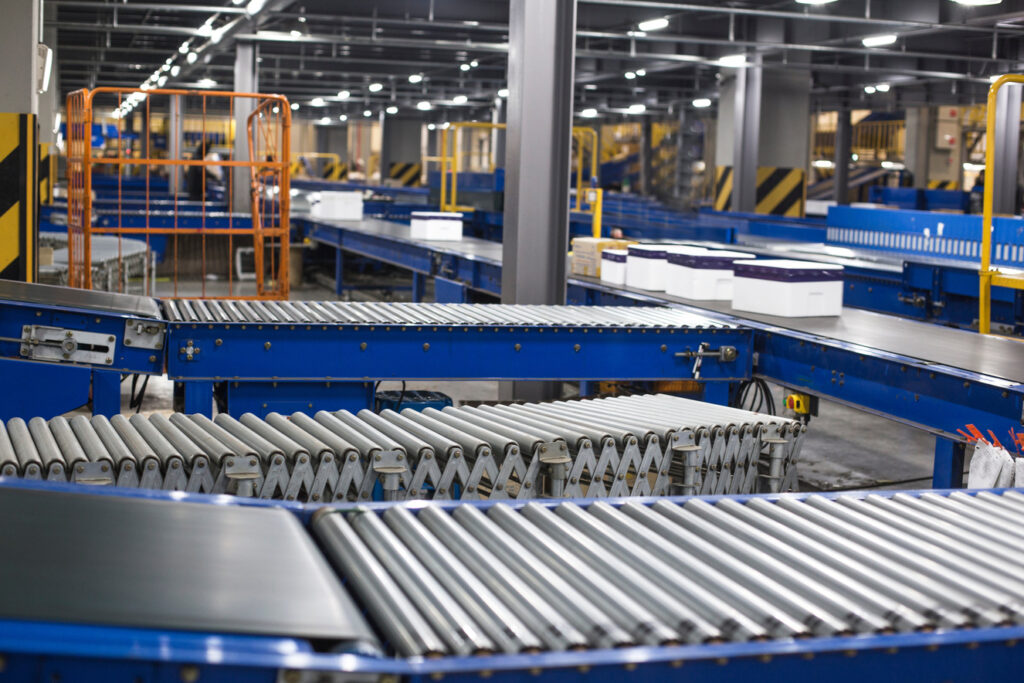
Greenspace Industrial – Leading the Warehousing Revolution
At Greenspace Industrial, we are committed to being at the forefront of the warehousing revolution. Our Automated Storage and Retrieval Systems (ASRS) and Vertical Lift Module (VLM) solutions, combined with advanced Conveyor and Sortation Systems, empower businesses to optimize their logistics operations, improve accuracy, and elevate overall efficiency. As a Warehouse Automation Company in Canada, we bring innovation to your doorstep, helping you navigate the challenges of the modern supply chain landscape.
In conclusion, the integration of Conveyor and Sortation Systems is a strategic move for any business looking to enhance its warehousing capabilities. By investing in advanced technologies and understanding the specific needs of your operation, you pave the way for a more efficient, accurate, and streamlined material handling process. Greenspace Industrial is here to be your partner in this transformative journey towards a future-ready warehouse.
Questions to Ask Before Implementing Sortation Systems in Your Warehouse Operations:
Before diving into the implementation of sortation systems, it’s crucial to conduct a thorough assessment of your warehouse requirements. Here are key questions to consider:
- Do I have any fragile items that need special consideration?
Understanding the fragility of your products is essential for selecting the right sortation system. Fragile items may require gentle handling and specialized mechanisms to prevent damage during the sorting process.
- What types of items do you need to sort? Is there a wide variety? Product geometry (size, weight)
Different products have varying characteristics, including size, weight, and geometry. Assessing the diversity of items to be sorted helps determine the appropriate sortation technology and configurations needed to accommodate your specific product range.
- What materials do I need for packaging? (bags, cartons, envelopes)
Packaging materials play a significant role in the sorting process. Whether you deal with bags, cartons, envelopes, or a combination of these, understanding the packaging characteristics ensures that the sortation system is compatible with your packaging requirements.
- Flat bottoms or uneven bottoms?
The bottom surface of your products can impact the sorting process. Some sortation systems are better suited for items with flat bottoms, while others can handle irregular or uneven surfaces. Knowing the bottom characteristics of your products ensures a seamless sorting experience.
- What sorting rate speed is required?
Sorting rate speed is a critical factor that directly influences the efficiency of your warehouse operations. Determine the desired throughput and sorting capacity to select a sortation system that aligns with your speed requirements and overall production goals.
- How much noise will this system create?
Noise levels in a warehouse can impact the working environment and overall employee satisfaction. Consider the noise generated by the sortation system and choose solutions that meet acceptable noise standards, creating a conducive and comfortable workplace.